What does Lean mean?
What does Lean mean? What does Lean stand for? What’s it all about?
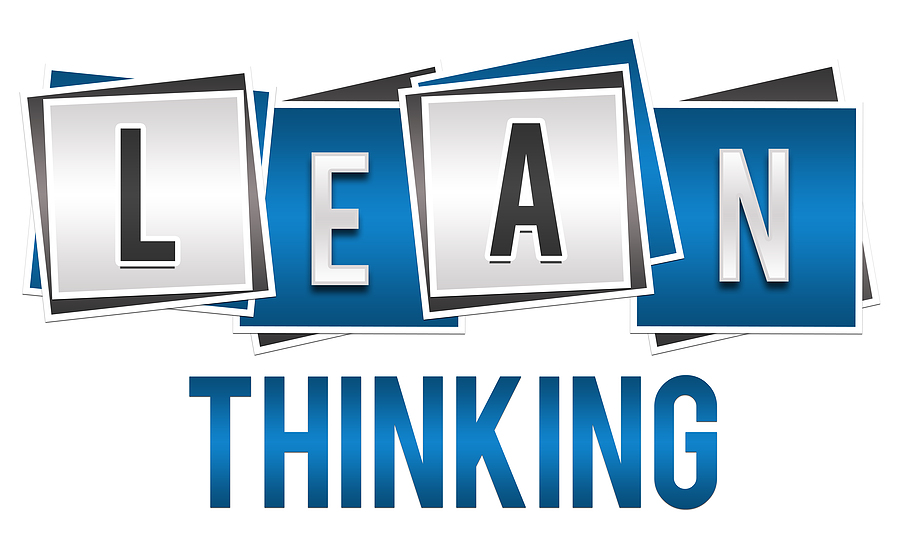
Good questions. To begin, ‘Lean’ is not an abbreviation, an acronym, or an initialism.
Okay, so what is LEAN?
Let’s get technical for a moment. The term ‘Lean’ was coined by John Krafcik, in his Triumph of The Lean Production System (Sloan Management Review; Fall 1988). He described the innovative production and management system he had seen at Toyota in Japan. Innovative in contrast to the production systems of many Western manufacturers throughout most of the post-war period, which were ‘buffered’ against virtually everything. Inventory levels were high, buffering against unexpected quality or delivery problems; assembly lines had built-in buffers to keep production moving should equipment fail; additional workers kept employed to buffer unexpected periods of high absenteeism; large repair areas to buffer against poor assembly line quality. At Toyota, it was the opposite; ‘buffers’ were minimal or non-existent, and ensuring quality was part of every role.
Now, that explanation may not entirely gel with people in sectors other than manufacturing, and it dates from 1988 Lean has moved on since then, spreading into virtually every sector including charity, government, health, higher and further education, law, medical research, philanthropy, and retail.
‘Okay, so how do you define what is Lean?’
There has never been one universally acknowledged succinct yet comprehensive definition of Lean. The definitions are, though, variations on a theme, often including elements, directly or implied, such as delivering value to customers, reducing costs, involving frontline employees, minimizing wasteful use of resources, reducing unnecessary activities and time scales, improving sustainability, improving quality, and problem-solving.
Okay, can you give me a definition anyway?
I can, the definition we created several years ago is, “The right people continuously searching for the simplest and smoothest process in order to meet customer needs perfectly.”
What does that mean?
I’ll explain; ‘The right people’ include those carrying out the work, particularly at operational and supervisory levels, and with the inclusion of ‘customer’, addresses the first of the Two Lean Fundamentals, Respect for People, ‘continuously searching’ addresses the second of the Two Fundamentals, Continuous Improvement, ‘simplest and smoothest’ cover the first four of the Five Principles of Lean – Value, Process, Flow, and Pull, and ‘perfectly’ covers the fifth principle, ‘Perfection’.
Alright, that sounds okay. You can tell me more about those fundamentals and principles later, but I’ve heard a few negatives about Lean.
Yes, I’ve heard those negatives as well, and in the past, I probably said and believed some of them, and then I discovered that Lean was not:
- About cutting employees or cutting costs
- Just a bag of tools
- A collection of techniques or best practices for you to simply copy
- The same as or part of or just another process improvement methodology
- Just a bunch of projects to deliver
- Just a computer thing
- Only for frontline employees
- Pushing employees to meet unrealistic or imposed targets
- Just about speed or efficiency
- Imposing a desired outcome
- Experts taking over and telling you what to do
- A cure for all organizational problems
- Quick and easy
Yes, they all sound familiar. I guess you have some positives for me now?
I certainly do. I discovered over time on my Lean journey that Lean was:
- A set of management practices based on the Toyota Production System
- A way of thinking and working
- Respectful toward everybody who participates in the process concerned: customers, employees, suppliers, the community, and so on
- About having the right resources in place and within reach
- Responding positively to the need to deliver more whilst consuming less
- Cultural change to deliver improved service and decrease costs
- About developing a sense of ownership, at all levels, for work
- Bridging silos, removing barriers
- An inclusive way to deliver sustainable outcomes
- Probably the best alternative to the old approach of layoffs and ‘cost-cutting’
- Outcome focussed
- And nothing to do with ‘mean.’
Lean is a Journey
“Of course, there’s a lot more to Lean than just a couple of lists about what it’s not and what it is.
What I discovered early on in my Lean journey was that while in my pre-Lean days, I may have had an understanding of some tools and techniques that I later discovered featured in the Lean approach, I did not know what many of those tools and techniques were called, nor how in many cases to correctly apply them, and in what order. And as to those Lean tools and techniques I did not know about, and the Lean philosophy itself, the Two Fundamentals and Five Principles, for example, well, I didn’t know about them. I guess I’m saying that my pre-Lean attempts at process improvement were, well, poor both in execution and outcome. Something you would want to avoid. If you want to know more about the Lean approach ….”
Regarding the …., I was thinking of some text to say, for example, “get in touch at” and point to either my website https://www.standrewslean.com or the Lab’s page https://agilestrategylab.org/solution/rapid-improvement-process/
Want to learn more about Lean?
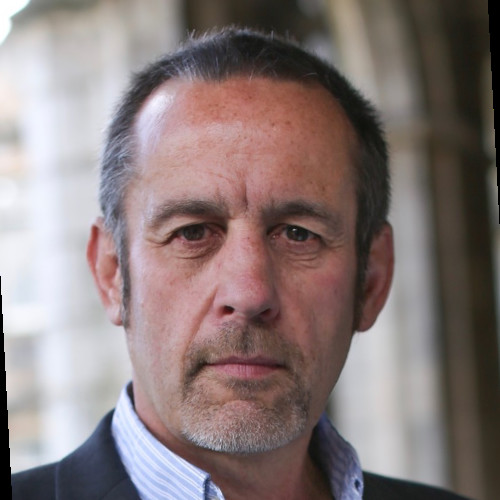
Mark is the Managing Director of St Andrews Lean Consulting. Mark, previously Director of Lean at the University of St Andrews in the UK, has over 15 year’s experience in the practical application of Lean process improvement. Mark enjoys transferring Lean skills by delivering training and in working with teams to help them dramatically improve what they had previously believed to be a problem process.