Third Thursday – January 2024 – Mark Robinson
Embarking on a Journey of Lean Process Improvement
About Our Third Thursday Guest: Mark Robinson
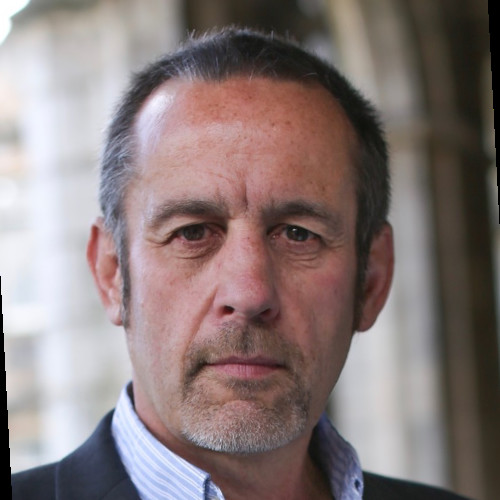
Mark Robinson is the managing director of St. Andrew’s Lean Consulting, with over 15 years of experience in lean process improvement. His expertise spans higher education and various service sectors worldwide. Formerly the director of lean at the University of St. Andrews in the UK, Mark is renowned for his methodical approach to process redesign and continuous improvement, helping organizations streamline operations and eliminate inefficiencies. He is an advocate for participant-driven process creation, emphasizing lean principles and respect for people in achieving optimal process enhancements.
Timestamp Overview
00:00 Mark Robinson, Lean Consultant with extensive experience.
03:43 Request to delivery: 10 days; minimal work.
08:50 Identify right people; follow sensible improvement process.
10:26 Identify goals, involve stakeholders, and document processes.
15:46 Non-valuating complies with laws, deviating from purpose.
17:23 Processes involve interconnected steps and necessary collaboration.
22:57 Focused on university convenience, not student needs.
27:27 Unnecessary steps in student confirmation process.
29:26 Travel requires planning due to unpredictable circumstances.
32:25 Streamline letter process: improve tech, permissions, automation.
37:43 Fund distribution processes often encounter challenges.
39:08 Lean is a structured process improvement tool.
Key Themes
- Importance of Planning
- Identify Current Practices
- Eight-Step Model
- Participant Involvement
- Continuous Improvement
- Respect for People
- Lean Process Efficiency
About the Conversation
Transforming Processes through Strategic Planning and Lean Methodology
In today’s fast-paced world, improving organizational processes can make a significant impact on efficiency and effectiveness. Mark Robinson, the managing director of St. Andrew’s Lean Consulting, recently illuminated the importance of strategic planning and the Lean methodology in driving successful process redesign. Here’s an in-depth exploration of his insights shared during a recent session hosted by Agile Strategy Lab.
The Blueprint of Process Redesign
Redesigning a process is much like planning a trip, as Robinson illustrated with his analogy of traveling from Edinburgh to London. The journey starts with a clear understanding of the current state. In process terms, this involves mapping out existing practices before moving towards improvements. Robinson’s eight-step model for process redesign begins with this crucial step.
Mapping the Present, Crafting the Future
The initial steps in the model involve thoroughly documenting the current state of a process. This is followed by gathering ideas for improvement and creating an ideal future state. The purpose is to envision the best possible outcome before constructing an interim state—a realistic and achievable improvement from the current to the ideal state.
Categorizing and clustering ideas plays an essential role in forming actionable steps for continuous process enhancement. This systematic approach ensures that improvements are not only planned but also practical and implementable.
Tackling Barriers with a “Wall of No Excuses”
Change is often met with resistance, which Robinson refers to as the “wall of excuses.” These common barriers to change hinder progress and must be addressed to foster a positive and resourceful mindset. Robinson promotes a “wall of no excuses,” encouraging teams to adopt a proactive stance against obstacles.
Success in Higher Education: Janyce Fadden’s Experience
Janyce Fadden shared her success story using this methodology in the context of higher education. By applying lean processes, Fadden experienced significant enrollment growth. This success highlights the versatility of Robinson’s model, which has been effectively applied in various communities, including universities and charitable organizations. The model demonstrates that wherever there are people and processes, there are opportunities for improvement.
Defining, Documenting, and Training for Success
Robinson emphasized the necessity of clearly defining a process’s start and end points. Without this clarity, it’s impossible to identify all necessary participants, objectives, and deliverables. However, many processes suffer from poor documentation, where the written procedures do not align with actual practices.
Training on Lean principles is integral to success. This training typically covers the fundamentals, principles, and common wastes found in processes. Planning meetings are crucial to ensure objectives are agreed upon, and resources are appropriately allocated.
Engaging Participants in the Process
A participant-driven approach to process redesign is paramount. Instead of imposing predefined solutions, Robinson stresses that guiding questions can help participants organically develop improvements. This ensures that the people who are most familiar with the process are directly involved in its enhancement.
Lean Methodology: Core Elements and Principles
The Lean philosophy is centered around two fundamentals: continuous improvement and respect for people. This approach is grounded in five principles—value, process, flow, pull, and perfection. To curb inefficiencies, Lean identifies eight common wastes: transportation, inventory, motion, waiting, overproduction, overprocessing, defects, and skills.
Continuous Improvement and Respect for People
The quest for continuous improvement necessitates regular updates to processes due to changing internal and external environments. Respect for people means engaging customers, suppliers, and employees directly in process improvements, avoiding top-down solutions that may not be effective.
Understanding and Standardizing Processes
Understanding the entire process flow is essential. All team members need to know upstream and downstream activities to ensure a seamless workflow. Standardized work procedures help align resources efficiently and minimize waste.
Efficiency and Balanced Workflows
Efficiency goals target achieving a balanced workflow, eliminating issues like batching and inefficiencies. The aim is to create a consistent workload across team members, enhancing overall productivity.
Real-World Applications
Robinson shared examples of reducing times for student request letters from ten days to mere minutes through process improvement. In a recruitment process case study, a team generated 457 improvement ideas, showcasing the breadth of potential enhancements.
Robinson’s approach encourages teams to take time away from daily tasks to focus on process improvements without distractions. This concentrated effort leads to meaningful and lasting changes.
Joining the Lean Journey
The Shoal Shift Team stands as a testament to the power of Lean processes, celebrating ten years of success. The invitation to join them in Alabama underscores the commitment to process excellence and the community’s role in achieving it.
In conclusion, Mark Robinson’s insights into Lean process improvement present a robust framework for organizations seeking to improve their operations. By understanding current processes, engaging participants, and fostering a culture of continuous improvement and respect, organizations can navigate the journey from inefficiency to excellence.